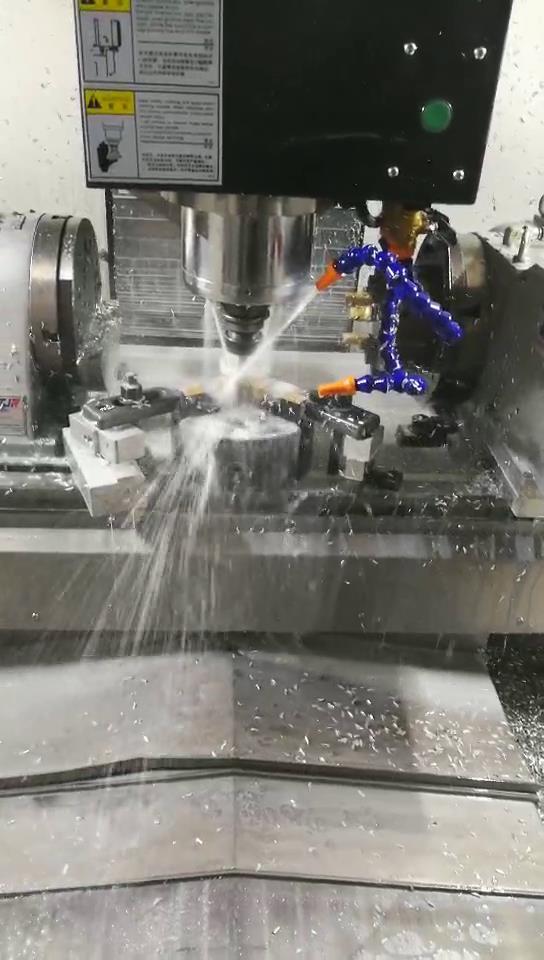
Casting is a widely used manufacturing process for creating complex-shaped and detailed metal parts. It involves pouring molten metal into a mold, allowing it to solidify, and then removing the finished product. The process is used to make a vast range of metallic components, from tiny intricate parts to large industrial machinery.
A casting parts manufacturer is a company that specializes in the production of metal parts using casting techniques. They have the necessary expertise, facilities, and machinery to handle the complex process of casting and produce high-quality and precise metal components.
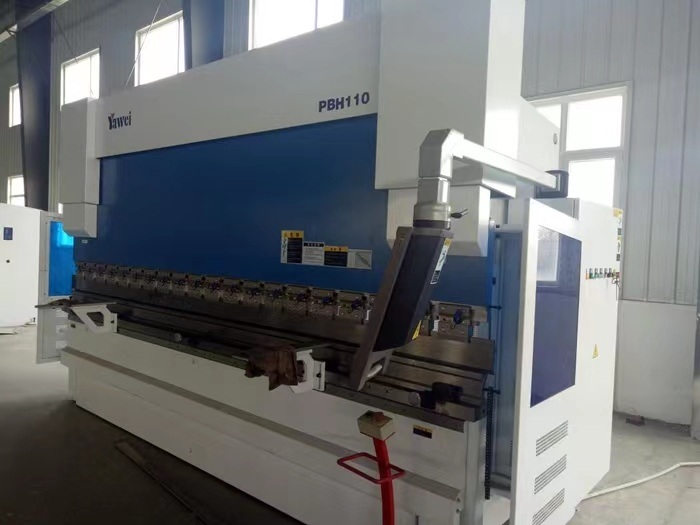
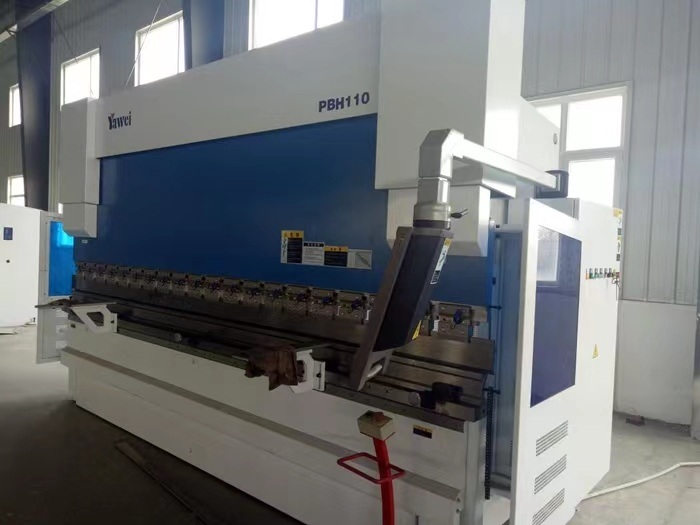
Casting Parts Manufacturing Process
The casting process has been around for thousands of years and has evolved over time. Today, modern casting techniques use sophisticated equipment and advanced materials to produce precision components.
The process starts with a design for the part to be cast. This design is then used to create a mold, usually made of sand or a ceramic material, which will be filled with molten metal. The type of mold used depends on the particular casting method employed, such as sand casting, investment casting, or die casting.
Before pouring the molten metal, the mold is prepared by coating it with a releasing agent to prevent the metal from sticking to the mold's walls. The molten metal is then poured into the mold, and the liquid takes the shape of the mold.
Once the metal has cooled and solidified, the mold is removed, and the cast part is ready for finishing processes such as trimming, sanding, or machining.
Types of Casting Parts Manufacturers
There are several types of casting parts manufacturers, each specializing in different casting methods and materials. These include:
1. Sand Casting Manufacturers: Sand casting is the most prevalent casting method, and sand casting manufacturers are the most common type of casting parts manufacturer. They use sand as the mold material, allowing them to produce large and heavy parts such as engine blocks, cylinders, and machine parts.
2. Investment Casting Manufacturers: Investment casting, also known as lost-wax casting, is a process in which wax patterns are used to create the molds. Investment casting manufacturers produce high-precision parts with intricate and complex designs. This method is often used to produce components for the aerospace, automotive, and medical industries.
3. Die Casting Manufacturers: Die casting is a fast and cost-effective method of producing large quantities of small- to medium-sized parts. Die casting manufacturers use a reusable steel mold, called a die, to create the parts and can produce a wide variety of shapes and designs.
4. Continuous Casting Manufacturers: Continuous casting is a specialized method used to produce long and continuous strips or rods of metal. Continuous casting manufacturers use a continuous process, pouring molten metal into a mold that is then cooled and solidified while continuously being extracted from the mold.
5. Centrifugal Casting Manufacturers: This method is used to create cylinders, pipes, and other tubular components. Centrifugal casting manufacturers pour molten metal into a rotating mold, and the centrifugal force pushes the metal against the mold's walls, creating a hollow tubular shape.
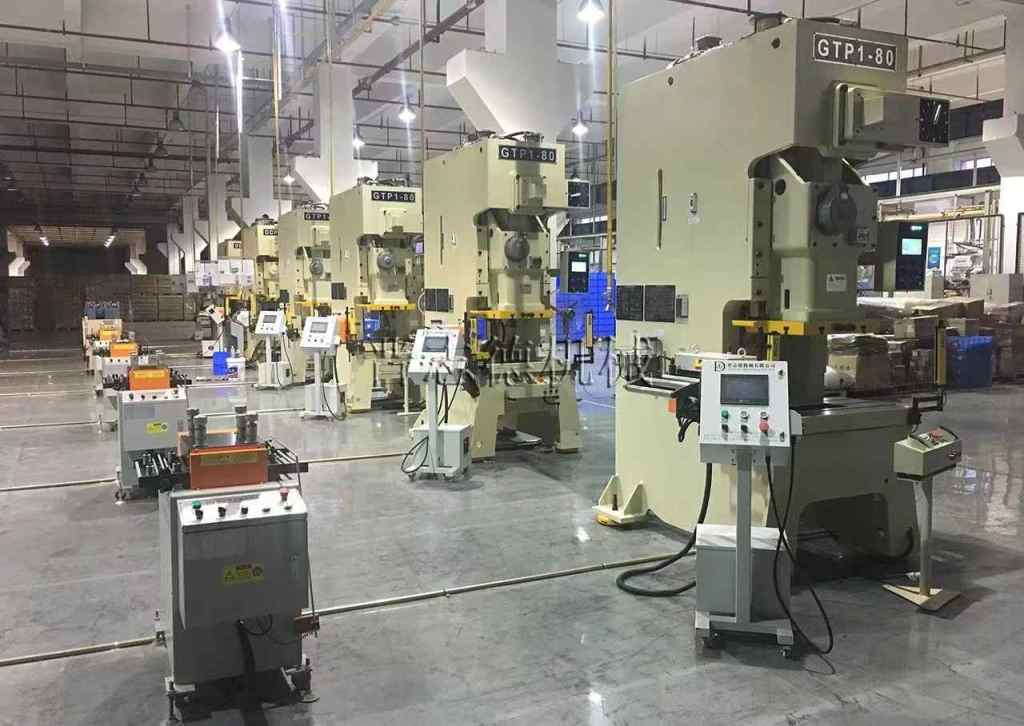
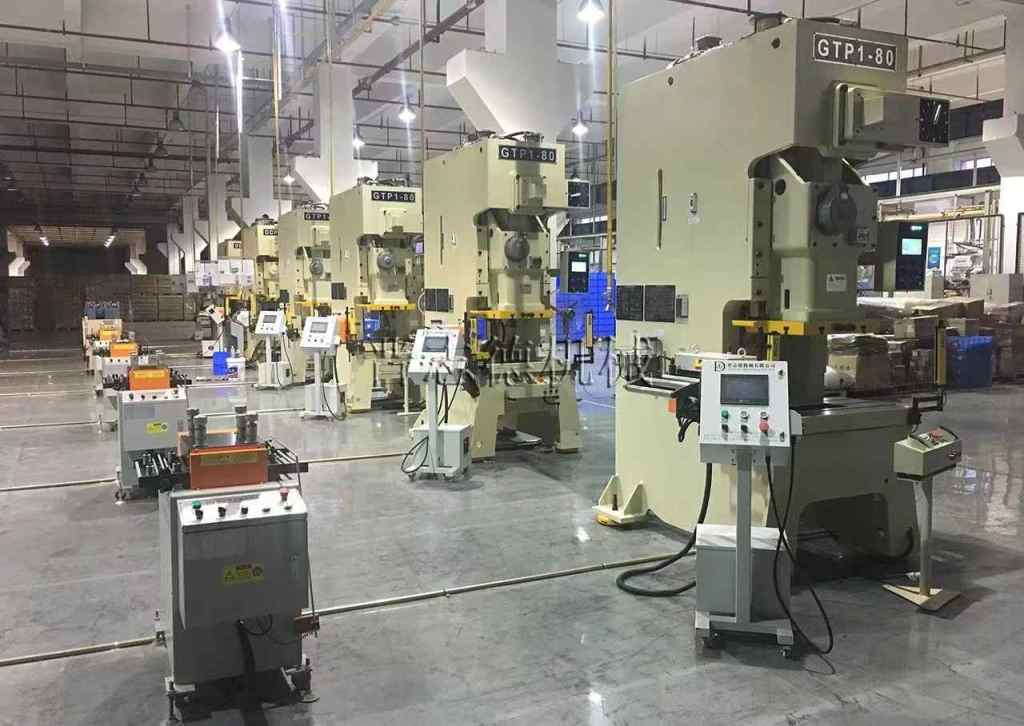
Benefits of Partnering with a Casting Parts Manufacturer
Partnering with a casting parts manufacturer for your metal part needs can bring significant benefits to your business. These include:
1. Cost Savings: Casting can be a cost-effective option for producing complex and detailed parts. It requires less finishing and machining, reducing the overall production costs. Additionally, casting parts manufacturers can produce large quantities of parts at a lower cost per unit.
2. Design Flexibility: Casting allows for intricate and complex designs to be accurately reproduced in metal. This gives designers and engineers more freedom and flexibility in their designs, resulting in more innovative and functional products.
3. Faster Production Time: With their sophisticated machinery and expertise, casting parts manufacturers can produce high-quality parts in a shorter amount of time compared to traditional manufacturing methods.
4. Consistency and Quality: With the use of molds, casting ensures consistency in the produced parts. This eliminates variations and defects, resulting in high-quality and accurate parts.
5. Material Variety: Casting allows for the use of a wide range of materials, including aluminum, iron, steel, copper, and more. This enables manufacturers to produce parts with specific properties and characteristics to meet the needs of different applications.